Understanding Heavy-duty Truck Exhaust Systems: Components and Emission Control
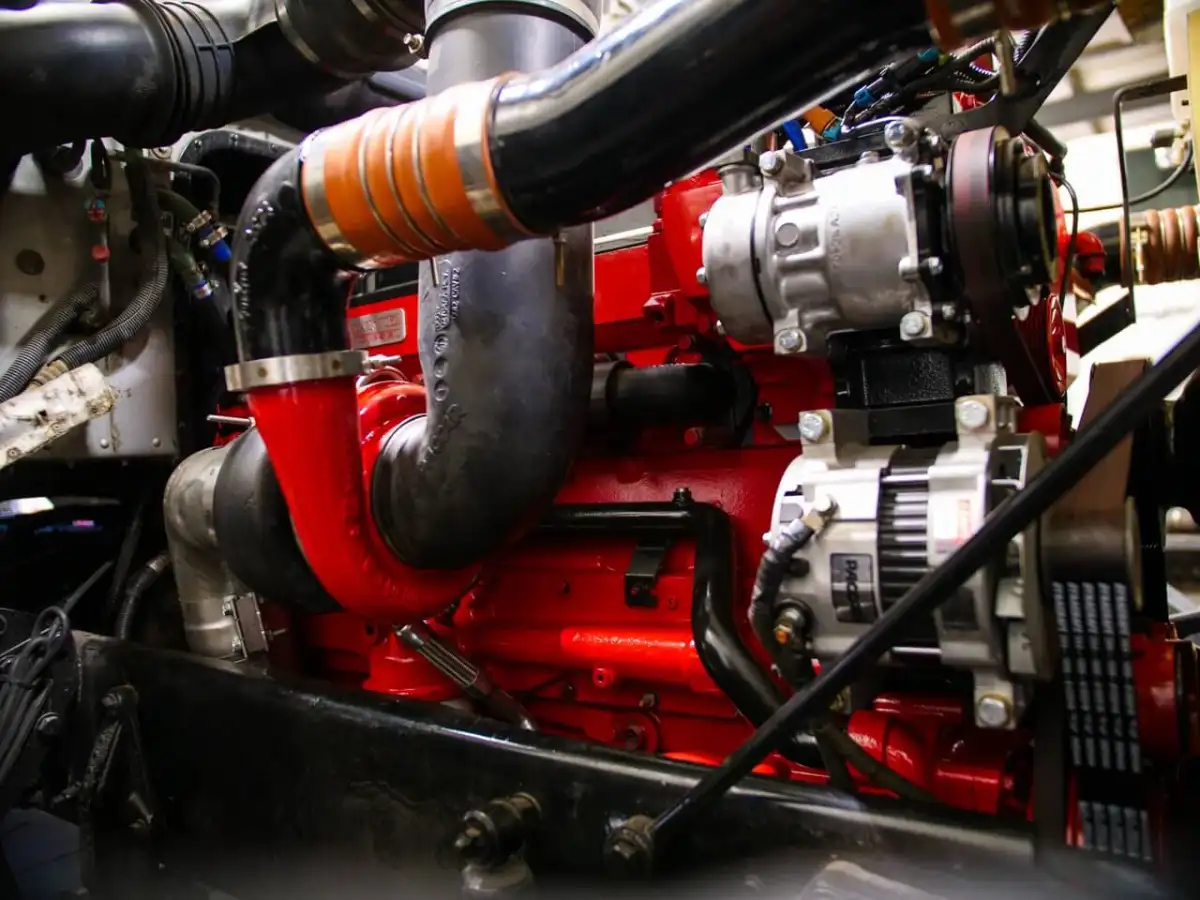
The exhaust manifold on a heavy-duty truck engine collects the hot exhaust gases exiting each cylinder and combines them into one outlet pipe. This allows for efficient transfer of the gases into the exhaust system. The manifold design aims to provide smooth exhaust flow by properly tuning the length and diameter of each branch tube leading from the cylinders. Even pulse distribution and crossover timing are ideal for optimizing cylinder scavenging.
Heavy-duty exhaust manifolds are constructed from durable cast iron or stainless steel to withstand the extreme heat and pressure pulses from the engine. Thermal expansion must be considered in the manifold design to prevent cracking. High-performance manifolds may utilize ceramic coatings to reduce heat absorption and lower surface temperatures for improved durability.
Catalytic Converter
Connecting to the manifold outlet, the exhaust downpipe routes the hot gases rearward through the system. The downpipe feeds into the catalytic converter which houses a honeycomb ceramic core coated in precious metal catalysts. As the hot exhaust passes through the converter core at high velocity, harmful pollutants in the gas flow undergo chemical reactions.
The catalysts transform carbon monoxide, unburnt hydrocarbons, and nitrogen oxides into less hazardous compounds of carbon dioxide, nitrogen, and water vapor through oxidation and reduction reactions. Diesel converters run at cooler temperatures than gasoline models and utilize specialized wash coat formulations to treat the diesel exhaust gases.
Converters must reach approximately 300°C before reaching light-off temperature where the catalysts become active. Efficiency approaches 90% once at operating temperature. Properly functioning converters are critical for reducing truck emissions to meet regulatory standards.
Diesel Particulate Filter
Downstream of the catalytic converter, a diesel particulate filter is installed to trap and incinerate soot and ash particles in the exhaust. Wall flow filter substrates capture particulate matter while letting gases flow through. The trapped soot and ash accumulate until burnt off when exhaust temperatures get hot enough during regeneration cycles.
Sensors in the exhaust stream monitor restriction levels and initiate active regenerations when needed to prevent clogging. Advanced regeneration systems inject fuel to elevate temperatures for actively oxidizing trapped particulates into CO2 and water when passive regeneration is inadequate.
Muffler
Further along the exhaust system, the muffler serves to reduce and tune the sound frequencies produced by the fast-moving exhaust gases. Perforated tubes, baffles, and sound absorbing materials absorb and dampen noises to acceptable decibel levels for legal road use.
Muffler designs aim to lower sound levels without causing excessive backpressure which would hinder engine performance and efficiency. Many heavy-duty mufflers utilize high-quality polished stainless steel resistant to corrosion and perforation.
Proper muffler sizing and tuning allows the engine to breathe freely while achieving target sound profiles. Dual mufflers may be used on large diesel engines to adequately muffle noise. Resonators further attenuate specific frequencies.
Exhaust Piping and Hangers
The full exhaust system is connected and supported by a combination of rigid pipes, flexible sections, and hangers. Smooth mandrel bent tubing allows gases to flow with minimal turbulence or restriction through elbow bends needed for routing around drivetrain components.
Exhaust tubing diameter and thickness is application-engineered based on expected thermal expansion rates, vibration dynamics, and gas flow volumes. Multi-ply flexible sections accommodate motion between fixed and moving parts. Hangers made from stamped steel or cast iron secure against sagging and fracturing.
Proper routing and support keep the exhaust system intact despite road vibrations, chassis twisting, and thermal cycling stresses over thousands of miles of use. Well-designed systems maintain sufficient flow rates through each component for efficient exhaust evacuation.
Maintenance and Repairs
Although durable when new, exhaust components wear and corrode over time, developing leaks or restrictions. Failed gaskets, eroded mufflers, clogged filters, and deactivated catalysts require repair or replacement to maintain proper function. Shops use 5-gas analysers to diagnose issues when trucks fail emissions tests.
Routine maintenance like filter cleaning helps prevent bigger repairs. Additives and ultrasonic devices reclog saturated filters by removing built-up soot and ash. Replacing restrictive mufflers and converters restores free flow and emissions control. Hangers, clamps, and tubing should also be checked for deterioration.
Exhaust Gas Recirculation
Many modern truck engines utilize cooled exhaust gas recirculation (EGR) to reduce NOx emissions. This involves re-routing a measured amount of exhaust gas back into the intake to lower combustion temperatures and available oxygen.
Cooled EGR systems use a heat exchanger to reduce the temperature of gases before mixing them with the fresh air charge. This increases density for improved combustion while limiting thermal NOx formation. Exhaust is recirculated through precisely calibrated EGR valves based on operating conditions.
EGR coolers and valves must be periodically cleaned to remove sticky soot deposits which can cause sticking and blockages. Proper maintenance keeps these components functioning per emissions calibrations.
Diesel Exhaust Fluid Injection
In addition to EGR systems, most late model diesel trucks use selective catalytic reduction (SCR) to treat NOx emissions. A special catalytic converter uses injected diesel exhaust fluid (DEF) to convert NOx into harmless nitrogen and water vapor.
The DEF fluid (urea and water mixture) is injected into the exhaust stream ahead of the catalyst where it thermally decomposes to form ammonia. This reacts with NOx on the catalyst surface for conversion into clean byproducts. Precise DEF metering and distribution ensures optimal emissions reduction.
DEF tanks need to be refilled when low to avoid disabling the truck. Extra tanks may be installed for extended range between fill-ups. Monitoring DEF quality and preventing contamination is critical for proper SCR system function.
Final Words
Keeping truck exhaust systems in top working order ensures engines run cleanly and efficiently. Components designed and sized appropriately allow the engine to breathe freely mile after mile down the road.
Contact Us
Supreme Truck and Trailer Repair is your go-to destination for all your truck and trailer repair needs. With our expert team, state-of-the-art facilities, and unparalleled customer service, we are dedicated to keeping your vehicles in optimal condition. Contact us today to experience the Supreme difference.